Increase asset lifetime and eliminate breakdowns with smart maintenance
Constantly monitor health of critical assets, calculate likelihood of failure and notify deterioration to relevant service personnel.
.
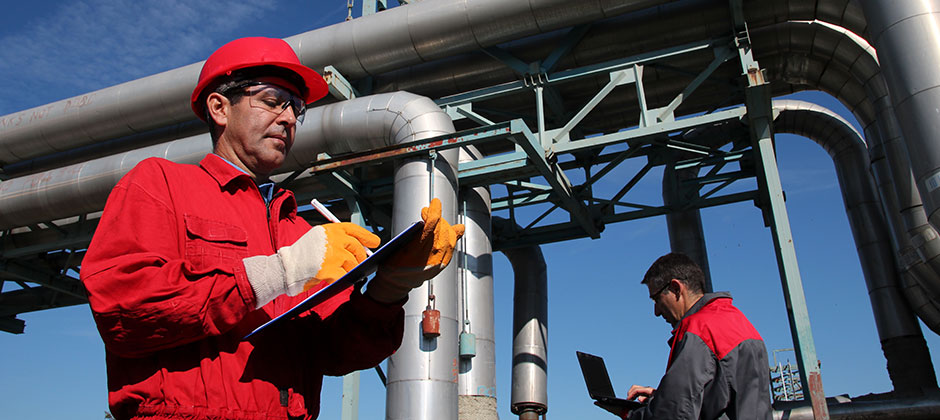
Predict Asset Failure
Eliminate Failure root cause
Plan Maintenance Better
Compare Multiple Assets
Increase Maintenance Effectiveness
Improve Product Quality

Install sensors to observe Machine Health
Automatically collect data about equipment health such as vibration, acoustics, temperature, energy consumption using sensors. These sensors push the data at fixed frequencies or on events to the central system where it is aggregated. The sensors are chosen and installed based on equipment form factor, environment constraints and operating conditions.
Model and Predict
Aggregated sensor data combined with failure events are used to model equipment behaviour and predict future failures. The prediction model is implemented on the industry leading solution from IBM. Real-time data is constantly fed into the model to improve the prediction accuracy.
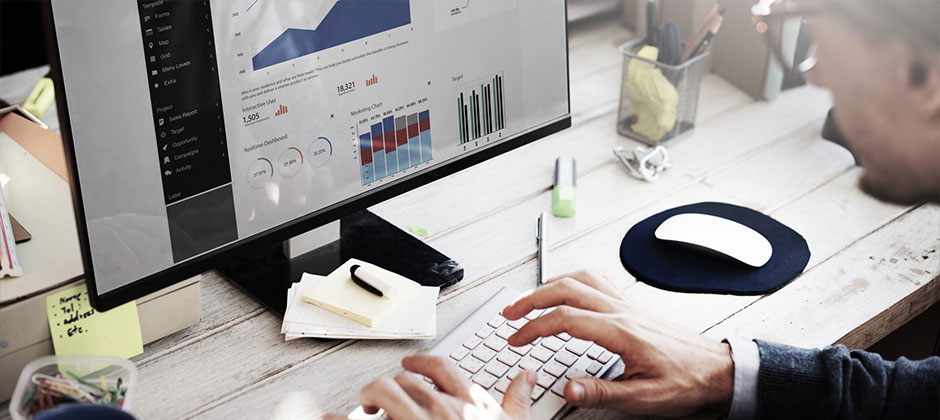

Integrate with Maintenance Planning
Failure prediction results provide most likely to fail equipment, estimated time between failures and probable root cause for failure. This information is sent to maintenance planners for targeted maintenance planning. Completed maintenance actions are provided to the predictive maintenance system for understanding equipment behaviour before and after maintenance.
Guide Maintenance Teams
Data related to likely failures, root cause and service effectiveness is pushed to maintenance personnel on their mobile devices for guided maintenance actions. Maintenance teams can also query equipment datasheets, work instructions and safety procedures from the system in an integrated manner.

Services
Need Analysis
Sensors Implementation
Analyse and Optimise
Operations & Support